В последние годы все большее распространение в различных отраслях промышленности находит сравнительно новая технология получения неразъемных соединений – сварка трением с перемешиванием (СТП). В настоящее время СТП широко применяется за рубежом в автомобилестроении, судостроении, вагоностроении, аэрокосмической промышленности. В частности, данный вид сварки широко используется для изготовления деталей, конструктивных элементов и модулей для самолетов, космических аппаратов и Международной космической станции такими фирмами как «Boeing», «Airbus» и « Thales Alenia Space. В нашей стране пионером применения СТП в серийном производстве, является ЗАО «Чебоксарское предприятие «Сеспель». На предприятии с использованием методом СТП изготавливают автомобильные цистерны-полуприцепы различного назначения из алюминиево-магниевого сплава.
В последнее время сварка трением с перемешиванием все чаще применяется для изготовления ответственных изделий, в том числе, цистерн для перевозки различных жидкостей и газов, сосудов, работающих под давлением, а также корпусных деталей ракетно-космической техники. Поэтому, развитию неразрушающих методов контроля для диагностики сварных швов, полученных данным методом, уделяется особое внимание.
Существует два метода неразрушающего контроля, которые позволяют обнаруживать дефекты в объеме сварного шва – радиография и ультразвуковая дефектоскопия, однако метод радиографии напрямую не позволяет определять глубину расположения дефекта. Это возможно сделать только с использованием дорогостоящих рентгеновских томографов, которые, кроме того, имеют существенные ограничения по размеру контролируемого образца, что делает невозможным их применение для контроля изделий крупного размера в промышленном производстве.
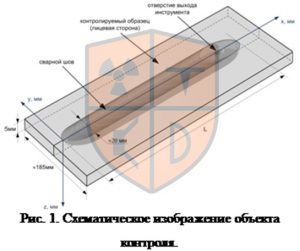
Решить задачу определения точного пространственного положения дефекта позволяет применение ультразвукового метода с использованием фазированных антенных решеток (ФАР). Отличием метода ФАР от традиционного ультразвукового метода является использование не одного, а нескольких расположенных в ряд или в виде двумерной решетки датчиков. Это позволяет фокусировать ультразвуковой луч за счет управления задержкой излучения сигналов каждым датчиком, а также осуществлять электронное сканирование сечения образца перемещением луча.
Целью данной работы являлась разработка методики обнаружения дефектов при ультразвуковом сканировании методом ФАР в сварных соединениях из алюминиевого сплава АМг5, полученных методом СТП.
Методика контроля
Образец для отработки методики контроля был получен сваркой трением перемешиванием из листов термически неупрочняемого деформируемого сплава АМг5М в отожженном состоянии (рис. 1). Сварка проводилась на опытно-промышленной установке ЗАО «Чебоксарское предприятие «Сеспель» [1].
Cваривались пластины толщиной 5 мм, ширина образца после сварки составляла »185 мм, ширина сварного шва »19 мм, длина сварного соединения »500 мм.
Ультразвуковой (УЗ) контроль осуществлялся с использованием дефектоскопа с фазированной антенной решеткой «HARFANG VEO 16:128» производства «Sonatest». Для ввода УЗ-луча в образец использовалась угловая призма X3-SB57-N55S производства «Sonatest» с углом ввода 360. В качестве пьезоэлектрического преобразователя (ПЭП) использовался 1D 64-х элементный ультразвуковой датчик ФАР X3-PE-10M64E0.6P производства «Sonatest» с частотой 10Мгц. Элементы в данном ПЭП расположены по одной линии. Одновременно для формирования УЗ-луча может использоваться 16 элементов.
Проведенные ранее исследования сварных соединений, полученных методом СТП, показали наличие специфических дефектов, присущих только данному виду сварки. Кроме того, было обнаружено, что скрытые дефекты при СТП, как правило, имеют значительно меньший размер по сравнению с дефектами, характерными для сварки плавлением. Поэтому, для проведения контроля был выбран ПЭП с частотой 10 МГц. Такая частота, с одной стороны, обеспечивает достаточную глубину прозвучивания, с другой стороны, позволяет выявлять дефекты минимального размера.
Так как лицевая сторона сварного соединения обладает выраженным чешуйчатым рельефом, а на корневой стороне возможно выдавливание зоны ядра, установка призмы непосредственно на шов с любой из его сторон не представляется возможной. Таким образом, для СТП швов, без дополнительной подготовки поверхности, невозможно использовать прямые призмы. Поэтому, для ввода ультразвукового луча в образец использовалась наклонная призма с углом наклона 360.
Особенностью сварных соединений, полученных методом СТП, также является большое соотношение ширины лицевой стороны шва по отношению к толщине свариваемых пластин. В частности, в данной работе исследовались образцы толщиной 5мм при ширине лицевой стороны шва 19мм. Из-за такой ширины шва не представлялось возможным установить призму ближе 9,5мм от осевой линии шва. Кроме того, из-за возможности наличия грата вдоль краев шва на лицевой стороне, необходимо отодвинуть призму еще на 1-2мм от края шва. В то же время, увеличение расстояния до шва увеличивает путь УЗ-луча до возможных дефектов, соответственно, уменьшает интенсивность отражений от них и вероятность их обнаружения. С учетом вышесказанного, призма устанавливалась так, чтобы расстояние от её переднего края до осевой линии шва составляло 11мм, и соответственно до края шва – 1.5мм.
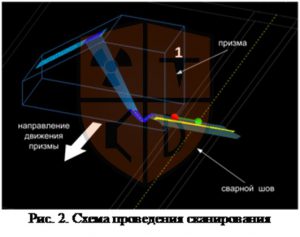
Для построения полной УЗ-дефектограммы методом ФАР с высоким разрешением необходимо получение последовательности секторных сканов сечений сварного соединения, перпендикулярных его осевой линии. Поэтому, для сканирования призма устанавливалась перпендикулярно шву и перемещалась с использованием электропривода с постоянной скоростью вдоль него от его начала до конца (рис. 2).
Секторные сканы (S-сканы) поперечного сечения шва записывались с одинаковым пространственным шагом по сигналам датчика пути, и строилась полная УЗ-дефектограмма сварного соединения. При записи дефектограмм, для достижения максимального пространственного разрешения вдоль линии сварного соединения использовался минимальный возможный шаг, который обеспечивал поставляемый в комплекте с дефектоскопом датчик пути – 0.2мм.
В методе ФАР для построения секторного скана, особенно при больших углах сектора сканирования и высоком угловом разрешении, необходимо проведение большого количества вычислительных операций в реальном времени, что ограничивает количество сканов, которые можно получить в единицу времени. Поэтому скорость перемещения призмы вдоль шва ограничена быстродействием вычислительной системы дефектоскопа. Она должна выбираться максимально большой, но, при этом, обеспечивающей запись секторных сканов с необходимым пространственным разрешением без пропусков. В данном случае такая скорость составляла около 2мм/с.
Для обеспечения ввода акустического луча в образец необходимо, с одной стороны, обеспечить минимальное расстояние между призмой и образцом, и с другой стороны, обеспечить присутствие между ними тонкой пленки иммерсионной жидкости. При недостаточном усилии прижима ухудшение акустического контакта может приводить к потерям сигнала на интерфейсе призма-образец. Избыточное усилие может привести к частичному или полному выдавливанию иммерсионной жидкости из зазора и к ухудшению либо потере акустического контакта.
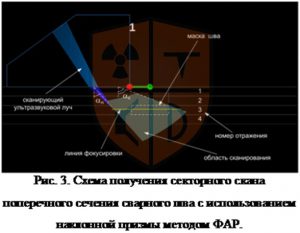
При разработке методики, усилие прижима определялось опытным путем. Для рассматриваемых условий контроля, оптимальная сила прижима, обеспечивающая необходимый акустический контакт, составила 10 Н.
Как было отмечено выше, особенностью СТП-сварных соединений является большое соотношение ширины шва и толщины свариваемых пластин. Это требует тщательного подбора угловых параметров ввода УЗ-луча в образец. Программное обеспечение дефектоскопа существенно облегчает эту задачу за счет наглядной визуализации процесса и отображения изменения параметров в реальном времени, в том числе в процессе сканирования. На рис. 2 приведена графическая схема получения секторного скана. Перед выбором параметров ввода луча в образец необходимо задать геометрические параметры сварного соединения для корректного отображения маски шва. Отображение положения призмы, маски сварного шва в нескольких отражениях, линии фокусировки и области сканирования позволяет подобрать линейку из 16 излучающих элементов ФАР, начальный и конечный угол ввода (aн и aк. на рис. 3) Согласно руководству по эксплуатации дефектоскопа, при углах ввода более 300, которые требуются в данном случае, для сканирования нужно использовать поперечную волну.
Начальный, конечный углы ввода, линейка излучающих элементов, положение и длина области сканирования в направлении распространения луча подбираются совместно, таким образом, чтобы в область сканирования попало всё поперечное сечение сварного шва хотя бы в одном отражении. При этом, нужно придерживаться следующих правил.
Сочетание параметров сканирования должно обеспечивать минимально возможное расстояние до контролируемой зоны с минимальным количеством отражений. Для этого стараются выбирать линейку из 16 излучающих элементов расположенных как можно ближе к переднему краю призмы. При этом, должно отсутствовать пересечение УЗ-луча с передней поверхностью призмы.
Необходимо добиваться минимального значения конечного угла ввода, так как при его увеличении усиливается затухание поперечной звуковой волны, а при больших конечных углах – переход части её энергии в энергию поверхностной волны.
Руководствуясь данными принципами для контроля СТП швов были подобраны следующие значения параметров. Для формирования УЗ-луча использовались элементы с 46 по 61. Начальный и конечный углы ввода составляли aн = 450 и aк = 650. При этом удалось добиться попадания маски шва целиком в область сканирования в 3 и 4 отражениях. Для обнаружения дефектов в сварном соединении, по нашему мнению, наиболее подходит вид фокусировки по постоянной глубине. В данном случае выбранное фокусное расстояние обеспечивало линию фокусировки примерно по середине высоты образца (толщины пластины) в третьем отражении (рис. 3).
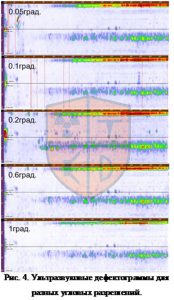
Ещё одним параметром сканирования является угловое разрешение, т.е. угол между двумя соседними дискретно формируемыми УЗ-лучами. Для исследования влияния значения этого параметра на возможность обнаружения дефектов были проведены сканирования образца с дефектом типа «wormhole», обнаруженным рентгенографическим методом, с угловыми разрешениями 0.050, 0.10, 0.20, 0.60 и 10. Полученные дефектограммы, представляющие собой «прозрачный» вид сверху сварного шва по длине, приведены на рис. 4. Обращает на себя внимание достаточно хорошая повторяемость дефектограмм, что свидетельствует о работоспособности разработанной методики и достоверности результатов дефектоскопии. Также хорошо видно, что наиболее полно и с максимальной интенсивностью дефекты проявляются при угловом разрешении 0.20. При больших и меньших угловых разрешениях интенсивность отраженного от дефектов УЗ-сигнала уменьшается.
Анализ дефектограмм показывает, что обнаруженный дефект в виде горизонтальной полосы примерно посередине представляет собой цепочку несплошностей тянущихся вдоль сварного шва на расстоянии 3-5мм от его осевой линии по наступающей стороне. В англоязычной литературе дефект такого типа носит название «wormhole»
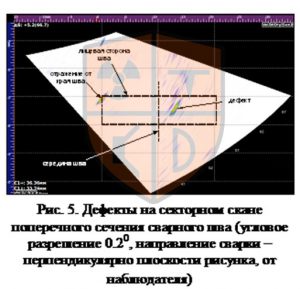
Появление дефекта в виде горизонтальной полосы вверху дефектограмм обусловлено резким перепадом высот между основным материалом и продавленным инструментом сварным швом на отступающей стороне.
Определить глубину залегания дефектов можно рассмотрев сечение дефектограммы, которое представляет собой скан поперечного сечения шва с использованием специального программного обеспечения, входящего в комплект поставки дефектоскопа. На рис. 5 такое сечение приведено в качестве примера. При корректном задании маски шва применение метода ФАР позволяет точно определить пространственное положение дефекта в сечении сварного соединения непосредственно по шкале дефектоскопа. В данном случае видно, что дефект типа «wormhole» находится на расстоянии 4мм от середины шва на глубине 2–2.5мм от поверхности на набегающей стороне шва. Еще один дефект – отражение от края шва, находится на лицевой стороне на краю шва с отступающей стороны.
Заключение
Проведенные в работе исследования показывают, что представленная методика, разработанная для ультразвуковой диагностики сварных соединений с использованием ФАР, полученных методом СТП является вполне работоспособной и может применяться для контроля швов. Это подтверждают данные дефектоскопии участка сварного соединения, которые свидетельствуют о хорошей выявляемости дефектов, повторяемости и достоверности полученных результатов.